7. Teil: Häufig verwendete Folien zum Drucken und Kaschieren
Einige typische optische Probleme bei der Kaschierung
von Karsten Schröder
Zusammenfassung
Optische Mängel bei der Kaschierung sind heute in vielen Fällen auf Unwissenheit bei der Entwicklung neuer Produkte und Bedienung der Anlagen zurück zu führen, da die meisten Probleme technisch eigentlich gelöst und bekannt sind. In diesem Teil diskutiert Karsten Schröder wichtige, immer wieder auftretende optische Probleme bei der Kaschierung von primären Kunststoffkaschierungen mit und ohne Aluminium oder Papier.
Ausgehend von Falten und ihren Ursachen, werden auch Bläschen mit ihren mannigfaltigen Ursachen beschrieben.
1 Kaschierfalten
Falten sind so alt wie das Kaschieren selbst – warum sind sie immer noch da? Ein Grund für Falten sind schwankende Qualitäten der Basismaterialien. Denn – wie entstehen Falten eigentlich?
1.1 Querfalten
Querfalten z.B. sind auf unterschiedliche Längen der Kaschierpartner zurück zu führen. Oft treten Falten im Randbereich direkt beim Zusammenführen der Folien auf. Diese stammen von so genannten Hängekanten eines oder beider Materialien. 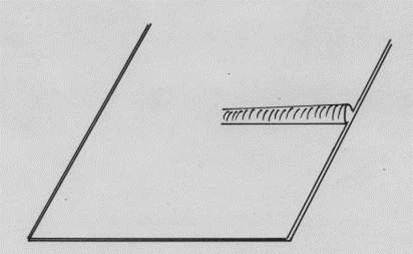
Gleicht der Maschinenbediener diese Hängekanten durch mehr Bahnspannung aus, so ist die Planlagetemperatur verschoben. Die Planlagetemperatur ist die Temperatur, bei der das ausgehärte Laminat plan liegt. Diese Temperatur ist besonders für die Weiterverarbeitung von Bedeutung.
Gleicht er diese Hängekanten nicht ausreichend durch mehr Bahnspannung aus, um die Planlagetemperatur korrekt einzustellen, kommt es zur Faltenbildung. Oft wird dieser schlechte Kompromiss in Kauf genommen in der Hoffnung: Die Wickelspannung wird es schon richten. Leider wird die Wickelspannung nur dazu führen, dass die Falte flach gedrückt wird und im besten Fall unkontrolliert verklebt. In jedem Fall können sich insbesondere bei Barriereverpackungen aus solchen Falten Delaminationen und Produktverderb ergeben – also kein „kleiner“ Mangel.
Ein Ausweg aus dem Dilemma ist zum einen das Wissen um das Problem und eine strikte Eingangskontrolle und Spezifikation der „Hängekantentoleranz“ Hierzu gibt es bisher mehrere, nicht genormte Verfahren. Prüfanweisungen hierzu können bei Innoform bezogen werden.
1.2 Längsfalten
Diese Falten in Maschinenrichtung ergeben sich entweder durch Materialmängel (Durchhang in der Mitte der Rolle) oder durch Maschinenmängel/ falsche Parameter an der Anlage.
Wird ein dünnes Material (z.B. PET-BO 12 µm) schon mit Längsfalten angeliefert, wird kein Kaschierer diese mehr ausbügeln können. In seltenen Fällen, eher schon bei dickeren, weicheren Folien, könne Breitstreckwalzen hier noch wahre Wunder verrichten, wenn mit optimaler Spannung gefahren wird – aber auch hier Achtung Planlagetemperatur.
In der Maschine entstehen Längsfalten ebenfalls durch mehrere Ursachen- Einige sind z.B. ein-/abgelaufene Walzen und Presseure, zu hohe Bahnspannung, zu grobe Walzenprofilierung bei dünnen Folien).
Für beide Faltenarten gilt: Vormaterialien machen einen Großteil der Problematik aus. Falten werden oft als Schönheitsfehler abgetan, können aber zu großen Fehlern bis hin zur Konsumentenschädigung durch Produktverderb führen. Falten können zusätzlich das Versiegeln von Verpackungen erschweren, wodurch sich zusätzliche Produktgefahren durch Undichtigkeiten ergeben.
Zusammenfassend ist also festzustellen, dass eine auf die leichte Schulter genommenen Faltenproblematik durchaus ernste Folgen haben kann. Falten sind vermeidbare und echte Kaschiermängel, die es in jedem Fall zu verhindern vermeiden gilt.
2 Blasenbildung
Blasen, Bläschen oder Kaschierflecken – egal wie man das Phänomen auch nennt – es ist vermeidbar und unschön. Es gibt eine Vielzahl von Ursachen für solche Fehler, die oft noch als leichte, optische Mängel (die oft toleriert werden) abgetan. Doch in vielen Fällen steckt mehr dahinter. Dort wo Bläschen zu sehen sind, ist die Verbundhaftung gestört und das kann auch zu technischem Versagen des Verbundes führen.
2.1 Wie sehen Kaschierbläschen und Kaschierflecken aus?
In den folgenden Abbildungen sehen Sie einige Aufnahmen aus unserem Labor, welche alle unter dem Sammelbegriff Blasenbildung zusammen gefasst werden können.
2.1.1 Regelmäßige, gleichmäßig verteilte Bläschen
Man sieht unter geeigneter Beleuchtung und geschultem Blick gleichmäßige, Stecknadelkopf kleine Flecken. Diese Flecken rühren von fehlendem Kontakt zwischen den beiden Kaschierpartnern her. Denn das Kleben bringt ja die beiden Partner eng zusammen, wodurch überhaupt erst eine Verbundhaftung und „Kontakttransparenz“ hergestellt wird. Ist dieser Kontakt nicht ideal, fehlt die o.g. Kontakttransparenz und das Auge nimmt diese Farbunterschiede abhängig von Farbton und Größe der Blasen wahr. Egal welche Blasen – das ist ein Alarmsignal für Kaschierer – das darf nicht passieren. Problematisch ist nur, dass einige Bläschen nach dem Aushärten verschwinden. Dieses ist durch Einwirkung von Wickeldruck bei Lösemittelfreien Kaschierungen oft der Fall, weshalb beim Kaschieren Bläschen gelegentlich unterschätzt werden.
2.2 Blasen aufgrund rauer Druckfarben wie z.B. weiß
Insbesondere in weiß bedruckten Bereichen findet man dieses Phänomen besonders häufig. Die Frage ist: Warum?
In der Draufsicht sieht man deutlich die grauen Flecken im weiß hinterlegten Bereichen. Das sind die Kontakttransparenz-Aussetzer“. Wie entstehen die und wichtiger – wie vermeidet der aufmerksame Kaschierer/Drucker solche Fehler?
Zum einen kann der Drucker eine geeignete, besonders fein gemahlene Druckfarbe verwenden, um die Rauigkeit des Farbfilms zu reduzieren, wodurch auch mit wenig Klebstoffmenge (1,8 bis 2,2 g/m² bei Lösemittelfreien Klebstoffen) gut und blasenfrei kaschiert werden kann.
In der Prinzipskizze wird verdeutlicht, wie sich zu wenig Klebstoff auf einer rauen Oberfläche (z.B. Druckfarbe) auswirkt.
Im folgenden Mikrotomschnitt sieht man ein weiteres Phänomen – der Klebstoff ist stellenweise gar nicht vorhanden. Es hat gar keine Benetzung stattgefunden. Das kann u.a. durch falsche Temperaturführung beim Auftragen, ungeeignete Kaschierpartner oder eine Druckfarbe mit zu geringer Oberflächenspannung entstehen. 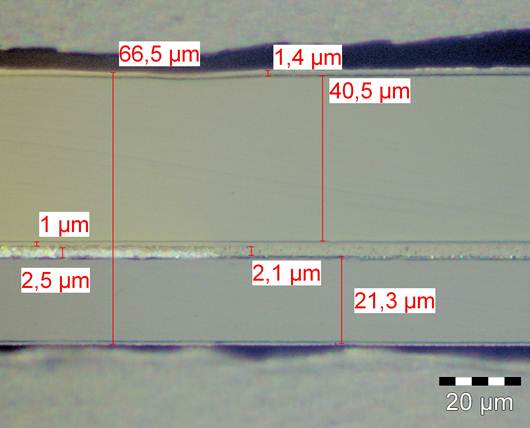
2.3 Gasblasen
Betrachtet man nun im Gegensatz dazu eine Gasblase, die durch das entstehende CO2, welches bei der Reaktion von Polyol und aromatischem Isocyanat immer entsteht, sieht der Schnitt etwas anders aus.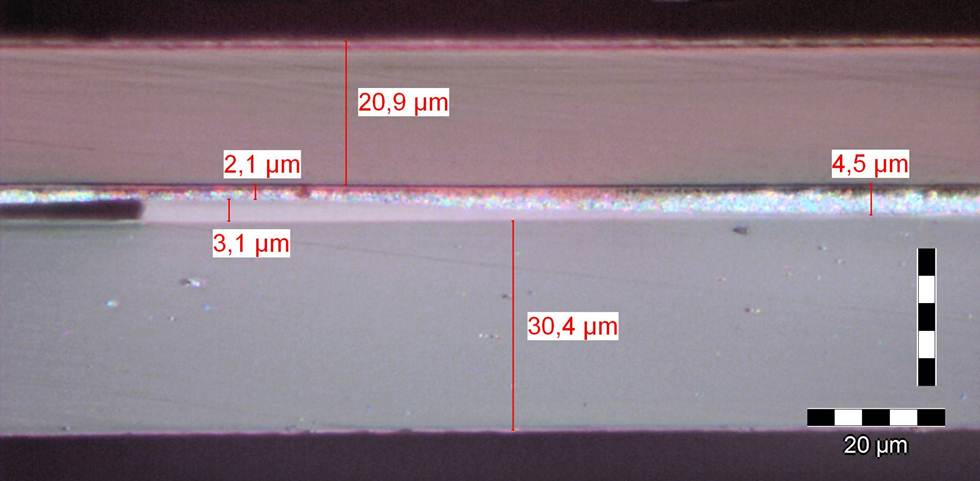
Hier ergibt sich am Rand der wesentlich größeren und unregelmäßigen Blasen eine Art Wulst, die dadurch entsteht, dass das Gas den Klebstoff verdrängt. Der Klebstoff sammelt sich aufgrund seiner Kohäsionskräfte am Rand der Blase und es entsteht dieser Klebstoffwulst.
Das gleiche Phänomen tritt auch bei partiellen Benetzungsstörungen auf, die durch Kontamination der Oberfläche oder ungeeignete Oberflächenspannung passieren kann.
2.4 Blasen aufgrund ungleichmäßigen Auftrags im “Mikrobereich”
Betrachtet man mittels Multiple Imaging Alignment nun einen stark vergrößerten Bereich einer Klabstofffuge im Mikrotomschnitt, so sind oft enorme Dickenschwankungen der Klebstoffschicht in der Praxis zu beobachten. 
In diesem Beispiel schwankt die Auftragsmenge auf einer Länge von 0,5 mm von 0,4 µm auf 4.4 µm (etwa = g/m²). Das kann nicht an einer falschen Walze oder schlechter Druckfarbe alleine liegen. Hier sind Rauigkeit und Oberflächenspannungseffekte mit im Spiel. Ein Lösungsansatz ist: Zunächst einmal die eigenen Produkte mit dem Mikroskop untersuchen, wie groß die Mikro-Schwankungen sind und ob Blasen sichtbar sind. Sollte das der Fall sein, kann das erneute vorbehandeln über dem Bedruckstoff schon Abhilfe schaffen, um eine möglichst hohe und gleichmäßige Oberflächenspannung zu erzielen. Zudem sollte die Viskosität des Klebstoffes variiert werden (durch Temperaturänderung), um den Einfluss dieses Parameters zu ergründen. Hier verhalten sich unterschiedliche Klebstoffe durchaus unterschiedlich auf gleichen Bedruckstoff und umgekehrt.
2.5 Stippen als Ursache für Blasenbildung
Auch Folien, Farb- oder Klebstoffstippen (Gels) können natürlich zu Kaschierfehlern führen, die sich als Blasen darstellen. Diese sind aber seltener pro Flächeneinheit und in der Regel deutlich größer.
Hier mal ein Beispiel einer Stippe in einer Folienschicht im Schnitt und Draufsicht: 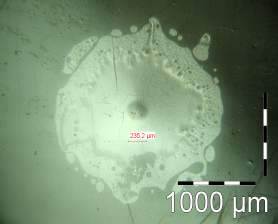
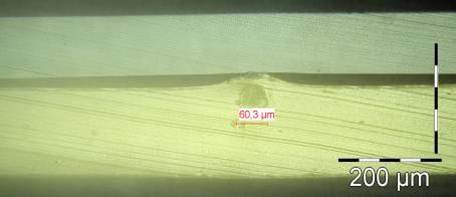
2.6 Gasblasen CO2
Die oben schon erwähnten, durch Gasabspaltung bei der chemischen Reaktion zwischen den beiden, das Polyurethan bildende Komponenten, Polyol und Isocyanat, sind oft groß (mehrere Millimeter im Durchmesser nicht kreisrund und meistens unregelmäßig verteilt.
Diese Blasen treten vor allem bei Gasbarrierefolien wie SiOx beschichteten oder metallisierten Folien sowie EVOH Sperrschichtfolien gehäuft auf. Hier können aliphatische, Klebstoffe oder einer Reduzierung der Auftragsmenge Abhilfe schaffen. Zudem sollte das System nicht zu schnell reagieren, so dass das entstehende Gas permeiren kann. Hier ist also eine Temperung/Warmlagerung eher kontraproduktiv. 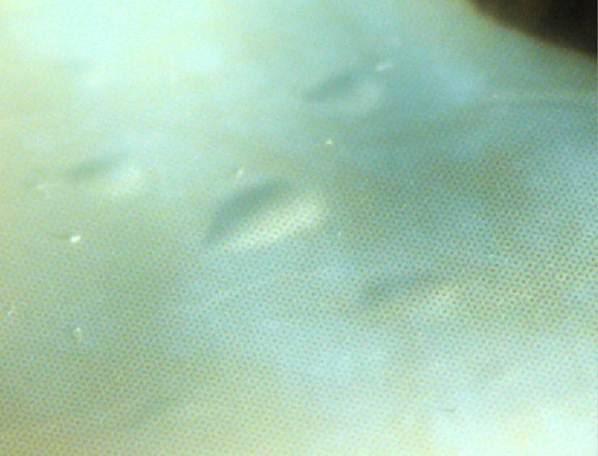
2.7 Gasblasen aufgrund einkaschierter Luft
Das Einkaschieren von Luft geschieht oft durch falsche Presseurhärte im Kaschierwerk. Ist der Presseur zu weich, entsteht enorme Walkarbeit, was zu Verbundstörungen führen kann. Ist er zu hart, werden Luftblasen nicht „ausgequetscht“ und dadurch nicht vermieden. Optimal wird üblicherweise eine Shore A Härte von 80 – 90° eingehalten. Was steht denn in Ihrem Wartungsplan für ein Sollwert und wie oft prüfen Sie die Härte eigentlich? 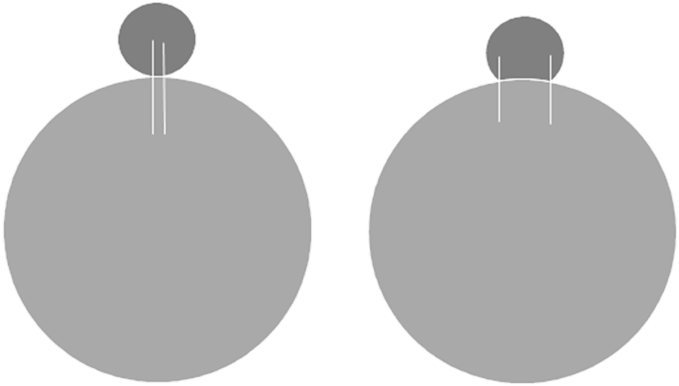
2.8 Blasen am Rand von Druckkanten
Sehr häufig finden sich Blasen am Rand von Druckkanten. Hier ist der Wickeldruck, insbesondere, wenn diese Kanten längs zur Laufrichtung verlaufen, geringer und Gase haben Platz sich zu sammeln. Hier helfen oft s.g. Stützlackierungen. Das sind transparente Lackierungen – meistens mit Verschnitt (= Farbe ohne Pigment), um diese Höhentoleranzen durch unterschiedliche Druckschichtdicken im Rapport oder in Längsrichtung auszugleichen. 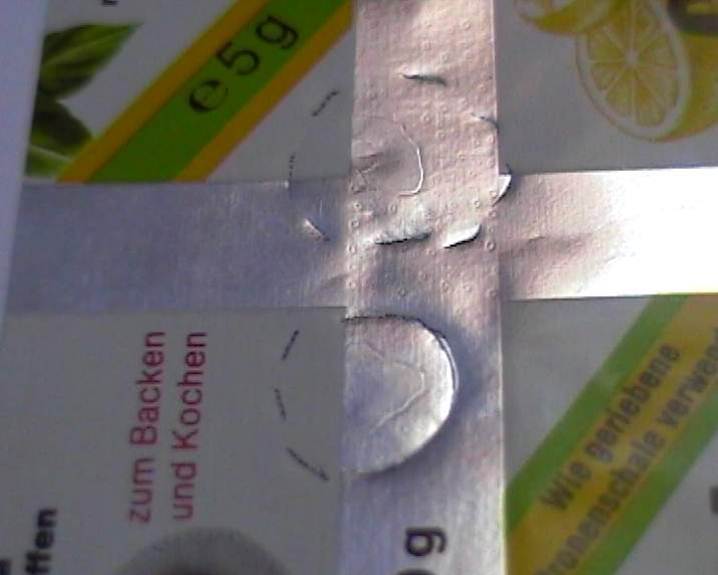
[Artikel Serie 1-8 “Drucken und Kaschieren” wird fortgesetzt]
P.S. Am 22./23. November können Sie uns auf der 2. Flexodruck-Tagung in Osnabrück treffen.
Dieses Mal dreht sich alles um: Ständig steigende Qualitätsansprüche und sinnvolle Lösungen?!
Es gibt völlig andere Themen und Erkenntnisse als vor 2 Jahren. Es hat sich viel getan.
Bilder, Videos und Experten Meinungen von der FD-Tagung stellen wir Ihnen nach der Tagung exklusiv auf unserer Facebook Seite zur Verfügung https://www.facebook.com/Innoform.Folienverpackungen?sk=app_247068188662059zur
zur Innoform XING-Gruppe: “Sichere Folienverpackungen durch Prüfen, Bewerten und Wissen mit Innoform”
Kontakt:
Innoform GmbH Testservice
Industriehof 3,
26133 Oldenburg
TS@innoform.de
www.innoform.de