“Prüfen und Bewerten von Folienverpackungen”
Permeation (Teil 6)
von Karsten Schröder (Innoform)
Der Einfluss von Feuchtigkeit, die in der Regel entweder aus dem verpackten Gut oder aus der Umgebungsluft stammt, kann erheblichen Einfluss auf die Sauerstoffbarriere (Sperrwirkung) einer Folie haben. Wann das ein Problem werden kann und welche Alternativen zur Verfügung stehen, wird hier erläutert. Zudem werden die beiden Begriffe „organische Barriere“ und „anorganische Barriere“ beschrieben.
1. Wann ist Feuchtigkeit für die Sauerstoffbarriere ein Problem?
Um zu wissen, ob Feuchtigkeit zum einen die Barriere verschlechtert und zum anderen überhaupt anwesend ist, muss man sich die Packungen selbst ansehen. Ist das Material denn überhaupt anfällig für einen Barriereverlus? – Denn darum geht es ja. Oder handelt es sich um ein Material, das gar nicht seine Barriere gegen Sauerstoff verändert, wenn die Feuchtigkeit im und um die Folie schwanken? Handelt es sich um eine organische oder anorganische Barriere? Mit anderen Worten ist sie feuchtigkeitsempfindlich oder nicht?
Und dann ist noch zu berücksichtigen, wie feucht denn nun die Barriereschicht wirklich wird und im schlechtesten Fall (worst case) werden kann.
1.1 Organische Barrieren
Kennen sie eigentlich den Begriff der organischen Barriere, der mehr und mehr Einzug in der „Barrierewelt“ und Folienindustrie findet? Gemeint ist in diesem Zusammenhang, dass die Barriere- oder Sperrschicht in der Folie aus Kunststoff (organischem Material) erzeugt wird. Beispiele hierfür sind Polyamid und vor allem Ethylen-Vinyl-Alkohol (EVOH). Die meisten – ja man kann sogar sagen bis auf PVDC alle üblichen Materialien – zeigen dabei ein Verhalten, das in der Praxis nachteilig sein kann. Und zwar immer dann, wenn Feuchtigkeit im Spiel ist.
Die Sauerstoffbarriere nimmt mit zunehmendem Feuchtigkeitsgehalt im Polymer (organischem Material) ab. Ich will hier nicht zu tief ins Detail gehen, aber doch erwähnen, dass man sich das Wasser als eine Art Quellmittel vorstellen kann, das den Abstand zwischen den Makromolekülen des Folienmaterials vergrößert und somit Platz für Permeation – also Durchdringen von Sauerstoff macht.
Die Abbildung zeigt, wie sich durch das „Einlagern“ von Wasser mehr Raum für die Permeation von Gasen – hier Sauerstoff, bietet.
Welche Polymere / Kunststoffe nun wie stark in der Barriere beeinflusst werden, hängt nicht nur vom Polymer selber ab, sondern auch von den Schichten, die es umgibt. Zur Vereinfachung und grundlegendem Verständnis, möchte ich hier aber nur prinzipielle Trends darstellen, die einfach in praktischen Versuchen dann quantifizierbar sind.
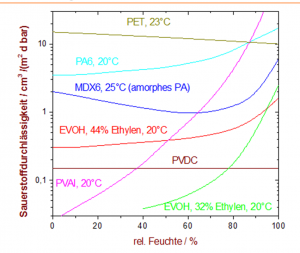
Das PVDC tanzt hier aus der Reihe, weshalb es auch so gerne für tiefgezogene also verformte Barriereschichten für feuchte Umgebungen oder feuchte Füllgüter eingesetzt wird.
Auch das PET verliert nicht die Barriere, wird aber aufgrund seiner eher weniger starken Sperrwirkung nicht wirklich als Barriere gegen Sauerstoff eingesetzt. Zum Einsatz kommt das PET z.B. als Material für thermogeformte Schalen, da die Materialdicken der Ausgangsfolien dicker sind und somit die Barriere besser.
1.2 Anorganische Barrieren
Im Gegensatz dazu spricht man von allen anderen üblichen Barriereschichten, wie z.B. die Metallisierung mit Aluminium, die Aluminiumfolie selbst oder Siliziumoxid (SiOx) bzw. Aluminium-Oxid (AlOx) bedampften Folien von anorganischen Barrieren. Diese sind nicht aus Kunststoff, sondern aus anorganischen Materialien wie Metall.
Das heißt allerdings nicht, dass es keine Folie wäre, sondern nur, dass die Sperrschicht oder Barriereschicht durch eine Nicht-Kunststoffschicht erzeugt wird.
Diese anorganischen Schichten haben nun den atemberaubenden Vorteil, dass sie bei allen Feuchtigkeiten nahezu die gleichen Sperreigenschaften behalten, die sie auch im trockenen Zustand haben.
Die folgenden Diagramme zeigen den Einfluss der Feuchtigkeit auf z.B. ein EVOH-Copolymer, wie es üblicherweise in vielen Fleisch-, Wurst- und Käseverpackungen verwendet wird:
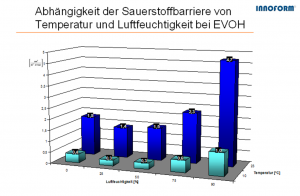
Und dann haben die anorganischen Barrieren noch einen grandiosen Vorteil, der alles andere überragt, aber in der Praxis kaum beachtet wird. Sie haben eine gute Barriere gegen (fast) alles. Sie sperren gut gegen Wasserdampf, Sauerstoff, Aromen, und manche sogar gegen Licht (Aluminiumfolie oder Aluminium-Metallisierung.
Nur verformen lassen sich die spröderen, anorganischen Schichten leider nur sehr wenig und zeigen doch auch immer wieder in der Praxis Knickbrüche in Falzkanten. Hier kann oft zwar durch geschickte Verbundstrukturen entgegen gewirkt werden, aber diese Eigenschaft ist immer mit zu beachten.
2. Fazit
Egal ob eine organische oder anorganische Barriere verwendet wird – es sind immer die Rahmenbedingungen der Anwendung für die Folienverpackung zu berücksichtigen. Wird ein warmes, feuchtes Klima in der Umgebung erwartet und es ist eine ausgezeichnete Sauerstoffbarriere erforderlich, so sind anorganische Barrieren vorzuziehen oder PVDC einzusetzen. Alle anderen Konstruktionen führen unweigerlich zu Herausforderung in Design, Struktur und Verarbeitung.
Sind hingegen thermische Verformung, Flexibilität und eine effiziente Herstellung wichtig, spielen die Kunststoffbarriereschichten (organischen Barrieren) ihre Vorteile voll aus. Wie bei allen Industrieprodukten gibt es hier auch innerhalb von Materialklassen signifikante Unterschiede hinsichtlich Barriere und Feuchtigkeitsempfindlichkeit. Hier gilt es also den richtigen Lieferanten mit dem richtigen Rohstoff zu wählen, um z.B. auch EVOH gefahrlos für feuchte Klimate einsetzen zu können.
Welche Schicht / welches Material welche Durchlässigkeit zeigt oder anders ausgedrückt, welche Barriere bietet, können Sie leicht online mit unserem kostenlosen Permeationsrechner ermitteln: http://www.innoform-testservice.de/tpages/tools/permeation.php Wenn Sie sich kostenlos mit Ihrer E-Mailadresse einloggen, sehen Sie sogar alle wichtigsten Barrierematerialien und können schon einmal virtuell ausrechnen lasen, wie diese sich im Verbund darstellen.
Ich freue mich wieder auf zahlreiche Kommentare und Anregungen für weitere Beiträge in unserer Innoform Expertenecke hier oder auf XING.
Freundlicher Gruß,
Karsten Schröder
P.S. Weitere Artikel zu diesem Themenbereich finden Sie nachstehend:
1. Kennen Sie eigentlich den Unterschied zwischen Dichtheitsprüfung und Permeationsmessung?
2. Was bedeutet eigentlich die Einheit cm³/m³ x d x bar bei der Permeationsmessung?
3. Was ist eigentlich die Permeationsrate?
4. Was gibt die Wasserdampfdurchlässigkeit eigentlich an?
5. Was bedeutet, die Folie hat eine gute Barriere?
Die nächsten Innoform Veranstaltung finden Sie HIER.
Innoform GmbH Testservice
Industriehof 3
26133 Oldenburg
www.innoform.de
TS@innoform.de